Industrial control, also known as an industrial control computer, refers to a set of tools that use a bus structure to monitor and manage production processes and electromechanical equipment. These systems are equipped with key computer features such as a CPU, hard disk, memory, peripherals, real-time operating systems, control networks, and user-friendly interfaces. Today, the main types of industrial computers include IPC (PC-based industrial computers), PLC (programmable logic controllers), DCS (distributed control systems), FCS (fieldbus systems), and CNC (computer numerical control systems).
Industrial Equipment Types
1. IPC: An industrial PC based on the PC bus architecture. According to IDC data from 2000, PCs make up over 95% of general-purpose computers. Their affordability, high quality, large production volume, and extensive software/hardware support have made them widely accepted by engineers. The core components of an IPC include an industrial chassis, passive backplane, and various plug-in cards like CPU and I/O boards. It is designed with all-steel casing, EMI filters, dual positive pressure fans, and EMC technology to address challenges like electromagnetic interference, vibration, dust, and extreme temperatures in industrial environments.
IPC Features
Reliability: Industrial PCs are built to withstand harsh conditions such as dust, moisture, temperature fluctuations, vibration, and corrosion. They typically have an MTTR (Mean Time To Repair) of around 5 minutes and an MTTF (Mean Time To Failure) of over 100,000 hours—far exceeding the 10,000–15,000 hours of standard PCs.
Real-Time Performance: Industrial PCs support real-time monitoring and control of production processes, allowing quick responses to changes in working conditions. They can collect data and adjust outputs immediately, something ordinary PCs cannot do due to the lack of watchdog functions and self-recovery capabilities.
Expandability: With a baseboard + CPU card design, IPCs can expand up to 20 boards, supporting various peripherals and modules for tasks like video surveillance, vehicle detection, and more, making them highly adaptable in industrial settings.
Compatibility: They support ISA, PCI, and PICMG resources, along with multiple operating systems and multi-language programming, enabling flexible integration into different environments.
2. PLC: A Programmable Logic Controller, or PLC, is an electronic system designed for industrial applications. It uses programmable memory to store instructions for performing logic operations, sequence control, timing, counting, and arithmetic tasks. PLCs control machinery or production processes through digital or analog input/output signals. As a modern control device combining computer and automation technologies, it replaces traditional relays and offers advantages like small size, easy maintenance, simple programming, high reliability, and strong anti-interference performance. Its versatility has led to widespread use across industries.
3. DCS: Distributed Control System (DCS) is a high-performance, cost-effective, and flexible solution for distributed control. It supports independent control systems, SCADA systems, and process management across various industries. Modular design, scalable hardware and software configurations, and ease of expansion make DCS ideal for power plants, steel mills, petrochemical facilities, and other industrial applications.
4. FCS: Fieldbus System (FCS) is a fully digital, two-way communication network that connects sensors, actuators, and controllers within a system. It serves as a local network for process control devices and smart instruments, offering embedded control capabilities for distributed applications. With over 40 international fieldbus standards like FF, Profibus, CAN, and HART, FCS is gaining popularity due to its flexibility and scalability.
5. CNC: Computer Numerical Control (CNC) systems use microprocessors or dedicated computers to execute control logic stored in memory. These systems interface with peripheral devices to perform precise machining operations. Modern CNC machines integrate advanced technologies such as mechanical manufacturing, information processing, automatic control, servo drives, sensors, and software, making them essential in precision manufacturing.
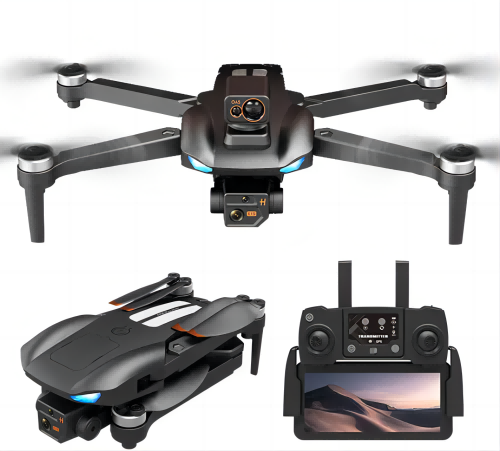
Photography Drone,High Definition Photography Drone,Three Axis Anti Shake gimbal High definition Photography Drone
Jiangsu Yunbo Intelligent Technology Co., Ltd , https://www.fmodel-ai.com