Editor's Note: The mercury release getter commonly used in fluorescent lamps is in the form of a strip, and the amount of mercury released is 30 mg/cm. For small or small power or cold cathode fluorescent lamps, the mercury yield is too large. Various micro-release mercury getters, the amount of mercury released can be between 0.5 and 5 mg/cm as needed, and how to properly store and use such mercury-sucking getters.
introduction
In recent years, there are many types of light sources that need to be filled with mercury, such as cold cathode fluorescent lamps for liquid crystal backlights, compact fluorescent tubes for self-ballasted fluorescent lamps, miniature fluorescent lamps, and nightlights. With the fierce competition between flat panel displays and color picture tubes, The corresponding backlights, whether LED or cold cathode fluorescent lamps, will expand rapidly.
Many micro fluorescent lamps require only 0.5 to 5 mg of mercury, which is equivalent to the weight of tiny mercury spheres with a diameter of 0.4 to 0.9 mm. It is difficult to control the dropping of such tiny mercury droplets into the lamp. Adding more mercury increases the cost of the material. On the other hand, there is more mercury polluting the environment when the lamp is broken or discarded. In addition, individual
The range of requirements for mercury filling of light sources is narrow. Therefore, the method of injecting mercury droplets is not practical, and a new method is required to quantitatively charge trace amounts of mercury.
In the T12, T8, T5 straight tube type fluorescent lamps, a certain proportion of the products are assembled with a stable titanium-mercury alloy with a predetermined amount of mercury released during assembly. The titanium-mercury alloy is easy to handle and Release of mercury. Usually, after the lamp is sealed off, the titanium-mercury alloy strip or ring is heated to (850 ± 25) ° C by the electromagnetic induction coil of the high frequency furnace for about 30 s, and the mercury is released from the alloy into the sealed space of the lamp. Of course, it can also be heated by a laser beam or infrared radiation.
1 Titanium-mercury alloy
Mercury and titanium are alloyed with Ti3Hg using a special process, first proposed by the Italian Engineering Suction Company (SAES) and referred to as the ST505 alloy, as shown in Figure 1, each mercury atom (in the center of Figure 1). Combined with 12 titanium atoms in the periphery. When the titanium-mercury alloy is mashed, ground into a fine powder and exposed to the atmosphere, the surface of each particle is surrounded by titanium atoms, which are oxidized to form a thin, tight and strong TiO layer, which forms an alloy. The body reacts with the atmosphere to obtain a barrier that hinders the release of mercury.
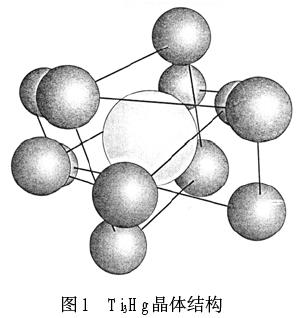
When the alloy is heated to above 500 ° C in a vacuum or an inert gas, TiO diffuses into the body. At the same time, when the mercury atom gains sufficient energy, it runs from the initial position in the crystal lattice to the outside. When it reaches the surface of the alloy, mercury escapes. This process is quite slow at temperatures below 600 °C, but when it reaches (850±50) It is very fast at °C. For example, when the titanium-mercury alloy powder-treated pellets are heated to (850±50) °C in vacuum or inert gas for 30 s, more than 70% of the total mercury in the powder can be released. The release reaches equilibrium during subsequent device operation, where the release rate is slower and is limited by the operating temperature. Figure 2 shows the mercury-amalgam mercury release versus heating and holding time.
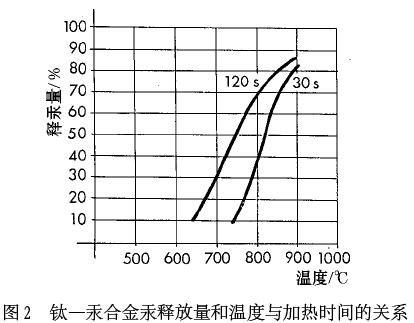
The amount of mercury obtained is related to heating power and heating time. The heating power is low, the temperature of titanium-mercury alloy is slow, the time for starting mercury release is too late, and the heating time required is long. As shown in the left curve of Figure 2, it needs to be heated for 120 s. In order to get 70% of the amount of mercury. On the other hand, if the power of heating the titanium-mercury alloy is high, the temperature rises quickly, and the time for starting the mercury release is earlier, the total heating time required is short, as shown in the right curve of Fig. 2, only heating for 30 s.
2 non-evaporable getter
Titanium-mercury alloys emit mercury, but titanium-mercury alloys are placed in air. As mentioned above, TiO is present. In order to perform high-frequency heating, the powder is usually applied to a metal strip or a stainless steel ring. When heating at a high frequency, the metal is first heated, and the powder is heated by heat conduction and heat radiation. Then, the stainless steel can absorb most of the adsorbed gas at about 850 ° C. These gases are harmful to the oxide cathode of the lamp. ,
Therefore it must be removed. If an evapotranspiration getter is used to absorb these gases, such as yttrium aluminum alloy BaAl4, the ruthenium evaporated at high temperature is placed on the wall of the lamp tube, which affects the appearance because black plaques appear in parts of the phosphor layer. Plaques in turn affect the luminous flux of the lamp, so it is not desirable. Therefore, it is desirable to use a non-evaporable getter to absorb the gas escaping from the metal during high frequency induction heating.
Conventional non-evaporable getters, such as sheet and wire zirconium or titanium, can only effectively absorb gases at temperatures in excess of 600-700 ° C, which greatly limits their range of use. However, by alloying with a certain amount of aluminum and zirconium, a getter material that acts at a lower temperature of 300 to 400 ° C can be obtained.
The aluminum-doped zirconium alloy greatly improves the gettering performance compared to the elemental zirconium. The optimum value of the alloy composition is Zr 84%, Al 16%, which is the composition of the getter alloy that SAES calls St101. In fact, St101 is composed of two intermetallic compounds: Zr3Al2, the main component, and Zr5Al3. Both can absorb reactive gases, and their presence greatly enhances the gettering characteristics of the alloy, which is higher than the sum of the two activities. This may have a different lattice from these intermetallic compounds.
Related to characteristics. For this reason, certain stresses are generated in the boundary regions of the two compositions, which makes the activity of these regions particularly large, and as a result, the bulk diffusion of gas molecules inside the alloy getter is much lower than the temperature required for the single element zirconium.
For 100% activation of St101, it takes 20~30 s at 900 °C, 4~5 min at 800~850 °C, 30 min at 750 °C, and 3 min at 750 °C. The activation rate is 60%, and if activated at 600 ° C for 30 min, the activation rate is 30%. Figure 3 shows the activation rate as a parameter, the relationship between activation temperature and time.
St101 The getter absorbed by the getter after activation is O2, CO, CO2, H2O, H2, etc., but does not absorb the inert gas.
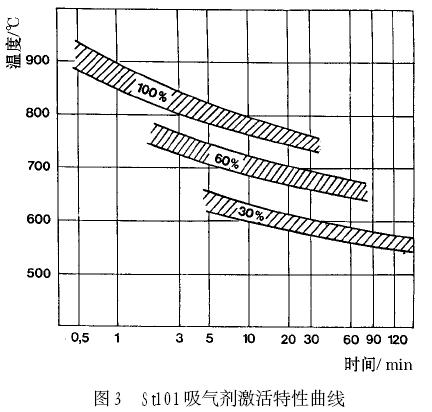
3 micro mercury release agent
In the 1980s, Nanjing Huadong Electronic Tube Factory introduced an aluminum release agent production line from SAES, Italy. The product produced by this line uses a metal base tape coated with St101 zirconium aluminum non-evaporable getter alloy powder on both sides of the metal strip. And St505 titanium-mercury alloy powder, this kind of absorbent type and mercury release agent coated on both sides of the metal base belt, the aspirated mercury release agent product, called "GEMEDIS", the mercury yield at that time was (30 ± 0.5) Mg/cm, the yield is too large for a mercury-filled light source such as a micro fluorescent lamp.
If St101 powder and St505 powder are mixed together in a certain ratio and then punched into different shapes to make a new mercury release agent, it is called “STAHGSORBâ€. This kind of mercury release agent is currently developed in the form of flakes and rings. There are three kinds of strips, which are suitable for liquid crystal backlights, small self-ballasted lamps, fluorescent lamps and other light sources and ultraviolet lamps for mercury release. These products are described below:
3.1 flake release agent
The St101 and St505 alloy powder is pressed into a sheet, as shown in Figure 4. The sheet does not support metal parts or metal containers. In order to obtain the minimum space to be placed in the lamp, it can be pressed into small pieces with a mercury release amount of 5, 3 mg or less, as needed, for special mercury gas discharge lamps. It can also be used in plasma display panels. The activation method can be induction heating, infrared radiation or a laser beam.

3.2 cyclic mercury release agent
The compact St101 and St505 alloy powder mixture is pressed into a ring-shaped aluminum release agent in a metal cup-shaped annular container. The ring-shaped container uses a nickel-plated iron belt, and the annular mercury yield is between 0.5 and 6 mg. High mercury yields can be prepared separately according to user needs. The high frequency induction heating method is used to activate the alloy, and Figure 5 shows the shape of the cyclic mercury release agent.
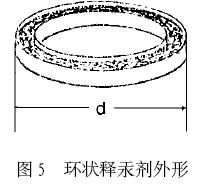
3.3 Pellet strip with mercury release agent
First, the nickel-plated iron strip is pressed into a groove at the position where the powder is prepared, and then the St101 and St505 alloy powder mixture is pressed into a pellet shape, and the pellets are evenly arranged in a regular manner, as shown in Fig. 6a, or two pairs each. The rules are arranged, as shown in Figure 6b, so that every two are cut open in the middle of the gap. Each individual pellet can produce approximately 1 mg of mercury. This pellet shape is particularly useful for miniature cold cathode tubes in which the nickel-plated iron strip serves both as a support for the pellet powder and as a cathode for the lamp.
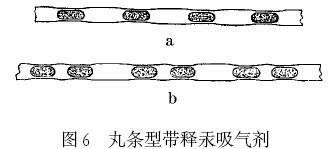
3.4 Micro GEMEDIS amalgam release agent
There are two types of GEMEDIS that can reduce the original mercury yield (30±0.5) mg/cm into a micro-mercury release agent. One is to use a metal strip narrower than the original product, and the St101 and St505 alloy powders are coated on both sides. That is, the micro GEMEDIS is made, and the mercury yield is 2.5~3 mg/cm, which is 1/10~1/12 of the original standard type. The other is that the St101 powder and the St505 powder are turned into discontinuous surfaces on the two sides of the metal paint of the above-mentioned miniature GEMEDIS product, and the pitch of the grooves is determined as 2, 3, and 6 respectively according to requirements. Mm, the mercury yield between the two scales is 0.5, 0.75, 1.5 mg/cm. This grooved strip is suitable for cold cathode fluorescent lamps, micro fluorescent lamps, compact energy-saving fluorescent lamps, etc. due to easy control during shearing. Figure 7 shows the product shape of the micro GEMEDIS and the grooved micro GEMEDIS mercury release agent belt.
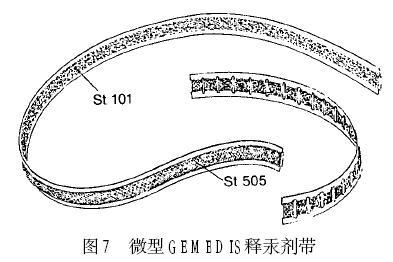
4 Precautions for use
The mercury-releasing getter is a powder that is pressed into a sheet or a metal alloy powder that is pressed on both sides of the metal strip or in the metal ring. If improperly handled during storage and use, it will cause little or no release of mercury. Mercury, the same getter will also lose its effectiveness. To do this, it is necessary to understand the problems that are avoided during use in order to use it properly.
4.1 Storage
The mercury release agent sold at the manufacturer is packaged in a sealed tank of protective gas or in a sealed container of desiccant. Such packaging allows the product to be stored indefinitely. Once the package is opened for use, if the package capacity cannot be used up at one time, the excess mercury release getter should be immediately placed in a vacuum storage cabinet to be vacuumed or placed in a glass tube to be vacuum sealed and stored. The drying device is sealed and stored in a dry state. Can not be placed in the atmosphere for a long time, the release of mercury in the atmosphere will lose powder and lose its effectiveness. Mercury release agent production plants are often shut down during the Huangmei season to ensure product quality.
4.2 Assembly welding
When the mercury release agent is placed in the light source, in order to prevent contamination of the product such as sweat, the hand needs to wear rubber or plastic gloves during use, and cotton yarn and nylon gloves are not allowed.
4.3 Sealing
When the lamp is sealed, try to avoid overheating of the assembled mercury release agent. If the temperature is too high, it is inevitable that the flowing nitrogen or inert gas can be used to remove the heat.
4.4 exhaust
When the lamp is exhausted, the temperature does not exceed 400~450 °C. This is to avoid premature release of mercury and partial aspiration saturation of the getter. If it is necessary to reach this temperature, the time to withstand high temperatures should be minimized.
4.5 Mercury release and activation
Usually mercury release and activation are carried out under high frequency induction heating, which involves the power of the high frequency furnace, the efficiency of the induction coil and the relative position of the coil and the mercury release agent, as shown in Figure 2, if the heated mercury release agent If it can't reach (850±50) °C, or it needs to reach 800°C after 1 min, it needs to extend the heating time, and it can't end within 30 s. Otherwise, the mercury release amount can't reach the specified amount, which will seriously affect the normal operation of fluorescent lamps. This involves process mastering issues and is independent of the quality of the mercury release getter. In addition, the mercury release step must be carried out after the lamp is sealed off to avoid contamination of the pump system and environment by mercury evaporation.
Edit; Nizi
7.2 Volt Battery Pack,Best 18650 Battery Charger,18650 Battery Size
Shenzhen Powercom Electronics Co., Ltd. , https://www.expowercome.com